Introduction
The tensile strength–strip method involves testing a specified width strip sample using a tensile testing machine with a constant rate of extension (CRE). The machine clamps and separates the sample at a defined speed until it breaks, recording both the breaking force and elongation at breaking.
Tensile Strength Of Fabric Test Standards
Adhering to standards such as ASTM D5034, GB/T3923.1-2013, ISO13934-1:2013, and ASTM D5035-11(2019) ensures accuracy and reliability in fabric tensile strength testing.
1. Sample Preparation
For woven fabric samples, a 5mm wide burr is reserved. The sample, cut parallel to the radial or weft direction using a custom-made cutting die (60mm*250mm long side), unravels its two test burrs to form a 50mm wide sample. In cases where fabrics cannot be removed from side yarns, a 50mm wide fabric sample is cut by shearing.
2. Fabric Tensile Strength Machine Requirements
The tensile machine must operate at speeds of 20mm/min and 100mm/min, with the capability to set grip widths at 100mm/200mm and an accuracy of ±1mm. The clamp surface must securely hold the sample without slipping or damaging it. Tensile strength testers use power control and data acquisition circuits to process force and elongation data, presenting tensile curves with a frequency greater than 8 times/S.
3. Fabric Tensile Test Procedure
Procedure variation depends on breaking elongation:
- Breaking elongation ≤ 75%: Use spacing 200±1mm
- Breaking elongation > 75%: Use spacing 100±1mm
Tensile speed elongation at break less than 8%: Use 20mm/min Tensile speed elongation at break 8 or more: Use 100mm/min
Adjust the grips position, set spacing to 200mm, and clamp the sample. The length direction should be parallel to the tensile direction of the tester. Configure gauge distance, speed, pre-tension, breaking strength, and elongation using the tensile tester software.
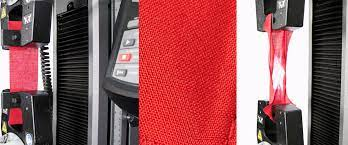
4. Result Analysis And Factors Affecting Fabric Breaking Force And Elongation
Analyzing breaking phenomenon, breaking strength, and elongation through tensile machine tests provides insights into fabric performance. Factors like original yarn strength, yarn density, and twisting can influence breaking strength. Fabric structure alterations, increasing interweaving yarns per unit area, and strategic finishing agents also impact fabric strength positively.
Conclusion
Understanding the intricacies of the tensile strength of the fabric–strip method is vital for ensuring quality and durability in textiles. From adhering to standardized testing procedures to comprehending the factors influencing breaking force and elongation, this process is indispensable for fabric manufacturers and quality control.
FAQs
1. How is breaking force measured in fabric tensile strength tests?
Ans: Breaking force is measured using a tensile testing machine, where a specified width strip sample is clamped and separated until it breaks. The force at which it breaks is recorded.
2. Why is yarn density important in fabric strength?
Ans: Yarn density influences the breaking strength of the fabric. Higher yarn density can enhance fabric strength by increasing the number of yarns per unit width.
3. What role does twisting play in improving fabric strength?
Ans: Adding twists to yarn can effectively enhance breaking strength. Twisting alters the yarn structure, making it more resistant to breaking forces.
4. How does fabric structure affect breaking strength?
Ans: The structure of the fabric is crucial; increasing the number of interweaving yarns per unit area can enhance fabric strength.
5. Can finishing agents improve fabric strength?
Ans: Yes, suitable finishing agents or strong protectants added in the finishing stage can help improve fabric strength.